Diaphragm pumps have become critical to many industries thanks to their versatility and durability. For a diaphragm pump to perform optimally, however, care must be taken during the materials of construction selection process. Even the most advanced pump designs can degrade and fail prematurely if the materials used for their components are incompatible with the liquid being transferred, particularly when handling abrasive or corrosive substances.
In the following guide, we’ll explain why using the correct components is crucial for safe, efficient diaphragm pump performance and operation. We’ll also discuss the chemical compatibility of various diaphragm pump materials so you can choose the best parts for your custom diaphragm pump.
Table of Contents
Material Selection in Diaphragm Pump Components: Why it Matters
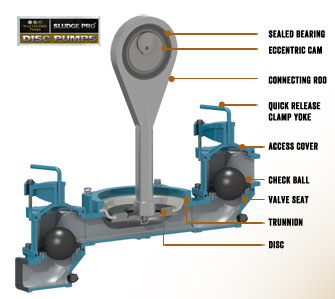
When selecting a diaphragm pump, most people understand the importance of buying from a reputable North American pump manufacturer. They also know to choose a manufacturer that offers an extensive selection of diaphragm pump spare parts for ease of maintenance. Beyond that, however, things get more complicated: Even when these criteria are met, using the wrong materials for the pump’s diaphragms, body, and other components can have multiple consequences.
Some of the potential issues associated with improper diaphragm pump material selection are outlined below:
Premature Wear & Tear
Operational inefficiencies and premature pump failure are the most common problems associated with improper material selection. Diaphragm pumps are known for their ability to handle a wide range of fluids. However, transferring abrasive fluids with the wrong parts can cause pump components to become scratched, worn, or clogged, for example, while corrosive liquids gradually reduce the structural integrity of certain metals and plastics. Choosing the correct diaphragm pump materials is, therefore, the best way to improve operational efficiency, reduce downtime, and lower maintenance costs.
Fluid or Environmental Contamination
One of the main advantages of using diaphragm pumps for industrial applications and wastewater treatment is their seal-less design. When a diaphragm pump is working properly, the diaphragms inside it act as a barrier that prevents fluid from leaking (either inside the pump or out into the environment). If the diaphragms stop functioning correctly due to improper material selection, however, this protective barrier is compromised. The pump may then slowly leach contaminants (such as toxic chemicals) into the product being manufactured or the surrounding area, or fail altogether, significantly disrupting operations.
In wastewater treatment, for example, the failure of a single pump can halt an entire operation and cost upwards of $500,000 per day. It can also cause harmful chemicals or bacteria to be released into the environment, damaging fragile ecosystems and threatening human health. As such, it’s crucial to ensure wastewater pumps can handle abrasion from suspended solids and exposure to corrosive chemicals. To illustrate, cast iron may seem like a strong material, but it corrodes quickly when exposed to the low-PH materials found in certain types of effluent. For these applications, stainless steel is a much more suitable choice.
Failure to Meet Regulatory Requirements
Some industries, such as the pharmaceutical, food and beverage, and oil and gas industries, maintain strict, specific pump material standards. All wastewater treatment systems in Canada must also conform to the effluent regulations established by the Fisheries Act. These standards are in place to ensure a hygienic processing environment for food, beverage, and pharmaceutical products. They also help prevent workplace hazards and the contamination of streams, rivers, and groundwater.
Failing to meet regulatory requirements often has devastating consequences. In the food and beverage industry, bacterial contamination can, in a worst-case scenario, lead to outbreaks of foodborne illness. More commonly, however, improper pump selection results in product inconsistencies, clogged machinery, and premature equipment failure. If a manufacturer chooses a pump with aluminum components to pump vinegar (an acid), for example, the aluminum will oxidize, reducing its strength. By ensuring you’re using a food-grade pump that meets current regulations, you can prevent these costly problems.
Workplace Safety Issues
In some circumstances, using the wrong pump materials can result in workplace injury or illness. Failing to use an ATEX-certified pump for certain oil and gas applications, for example, increases the risk of fire and explosion. ATEX-certified pumps are also designed to be airtight, so workers are protected from harmful dust and fumes.
Chemical Compatibility Guide
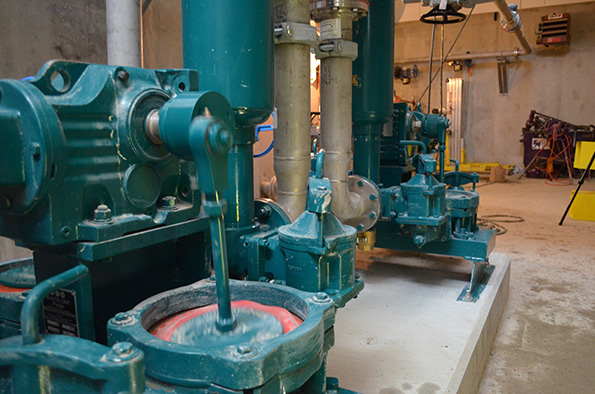
At Wastecorp, we offer comprehensive diaphragm pump customization options so our customers can choose the best compatible materials for their specific applications requirements. For in-depth information on the various diaphragm pump configurations available at Wastecorp, consult our guide to selecting the right diaphragm pump. Or, read on to learn more about the most common diaphragm pump materials:
Choosing the Right Materials For the Pump Body
When configuring your diaphragm pump, you’ll have the choice of a metal or plastic pump body. As a general rule, plastic pump bodies are recommended when transferring corrosive liquids, whereas metal pump bodies provide superior abrasion resistance.
Some of the best pump body materials for use with chemicals include:
Ductile iron. For mild caustic substances (between pH 4-5 or 9-10), ductile iron is the preferred choice because it’s extremely durable and can be grounded. Many wastewater treatment pumps contain ductile iron.
Stainless steel. Stainless steel combines broad chemical compatibility with superior abrasion resistance, surface smoothness, and groundability. For this reason, many pumps designed to meet sanitary requirements, such as food and beverage pumps, feature a stainless steel body.
Acetal (also known as polyoxymethylene or POM). Acetal is a strong, durable, low-friction engineering plastic. It provides excellent resistance to solvents, but it is not suitable for use with strong acids or bases.
Polypropylene. Polypropylene is a budget-friendly material that offers moderate resistance to acids and bases.
Kynar (also known as PVDF or polyvinylidene fluoride plastic). Kynar offers unmatched resistance to strong acids and bases but at a much higher cost than polypropylene.
Selecting the Best Valve Seats, Balls, and Diaphragms For Your Diaphragm Pump
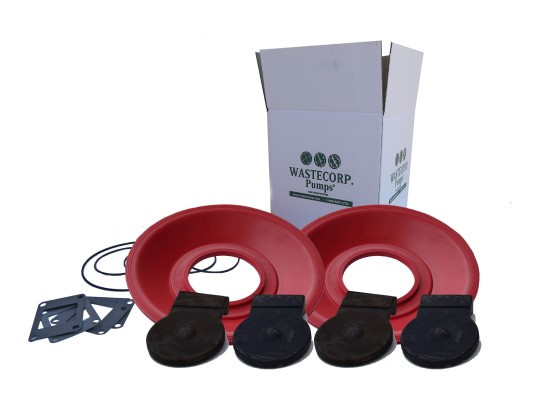
Because diaphragms play a crucial role in how AODD pumps and their engine-operated counterparts transfer liquid, a wide variety of configurations exist for diaphragm plates, seats, and balls.
Some of the most popular materials for these components include:
Santoprene. Santoprene is considered one of the best diaphragm materials because it’s light, pliable, and strong – qualities that give it an extremely long flex-life. This material also offers moderate to high chemical resistance, making it suitable for multiple applications. However, because Santoprene is light, it should not be used for valve balls when transferring highly viscous liquids.
EPDM. EPDM rubber can withstand very cold temperatures and is suitable for use with dilute acids, caustics, and abrasive substances, though it has a reduced flex-life compared to Santoprene. This versatile material is often found in sanitary pumps used in the food and pharmaceutical industries. EPDM is also a popular choice when transferring paints and coatings as it can withstand the abrasive metal flakes included in many paints.
Buna-N (nitrile rubber). Another highly flexible diaphragm material, nitrile is typically used with very abrasive substances, but it also offers mild chemical resistance. Nitrile may also be combined with stainless steel to create valve balls that seal quickly.
Viton (FKM). For very aggressive chemicals, Viton is the recommended choice, though it comes with a high price tag. Unlike other rubber compounds, Viton can safely handle most highly corrosive and toxic substances, including acids and various hydrocarbons.
PTFE. A durable, chemically inert material, PTFE is suitable for use with many non-abrasive substances, including highly aggressive chemicals. PTFE is compatible with corrosive fluids (including aromatic or chlorinated hydrocarbons), caustics, ketones, acetates, and potent, undiluted acids. This material is also smooth and heat-resistant. Many sanitary pumps utilize PTFE because it can be cleaned with steam or boiling water.
Because PTFE is somewhat inflexible, it’s typically used for ball, valve seats and other rigid diaphragm pump components where extreme chemical resistance is required. In some cases, however, it’s combined with a more pliable material to create diaphragms.
Hytrel (TPE). Hytrel offers better abrasion resistance than PTFE while still being able to withstand multiple chemicals. Hytrel can effectively process oils and hydraulic fluids, along with acids, bases, amines, and glycols. However, Hytrel offers limited temperature resistance, with an operating limit of 70 degrees Celsius in most situations.
Many pumping applications require the careful combination of multiple materials optimized for flexibility, longevity, and temperature resistance. A standard Wastecorp Mudsucker Diaphragm pump model, for example, might feature a reinforced neoprene diaphragm combined with a heat-treated aluminum A356 pump casing, EPDM flapper valves, and carbon or stainless steel pump rods and crank arms. However, this configuration may vary considerably based on job requirements. For advice about the specific materials needed for your application, ask our experts for a free consultation.
To check the properties of various materials, you can also refer to our convenient online chemical compatibility guide. Using this tool, select from a variety of materials listed for an overview of which substances it can safely interact with. You can then use this information to streamline the process of customizing your diaphragm pump.
Conclusion
Understanding the chemical compatibility of different diaphragm pump materials is crucial to ensuring regulatory compliance, supporting a safe workplace environment, and minimizing repair costs. Before customizing a diaphragm pump, thoroughly review the properties of the liquid you plan to transfer, including its chemical composition, temperature, viscosity, and abrasiveness. Then, choose the appropriate parts based on safety considerations, industry standards, chemical compatibility, and cost-effectiveness for optimal lifetime performance.