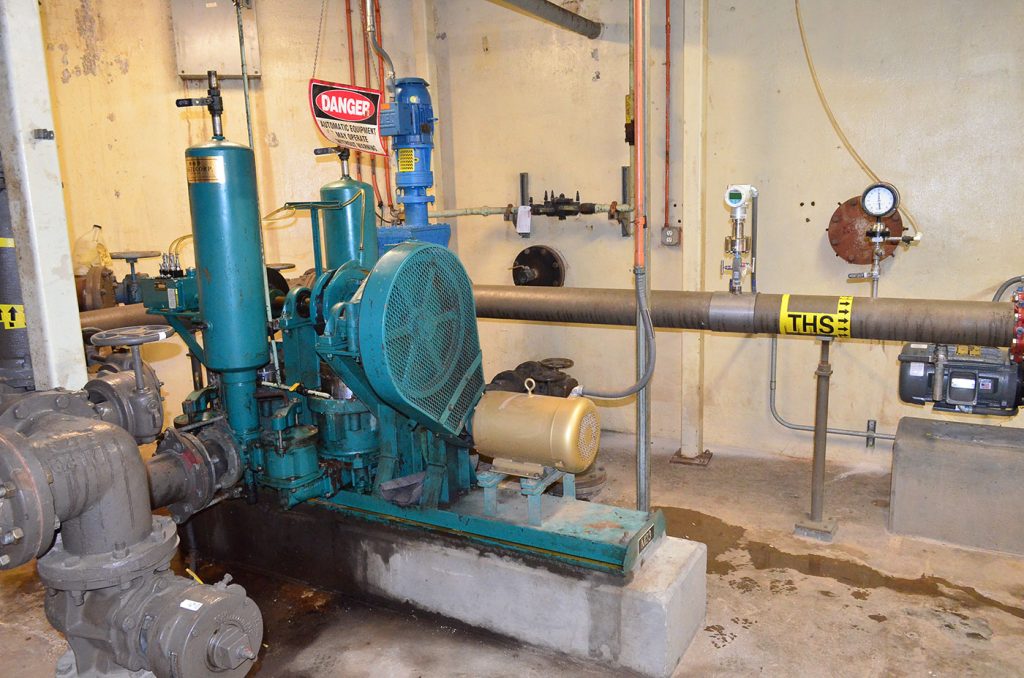
Food waste to energy applications are popping up all over the USA and Canada. The general idea is to take food waste, including restaurant waste like grease trap oil, cooking oil, seafood shells, meat, vegetable matter, animal fat and convert it into fuel for cars, homes and businesses. The process to do this requires a variety of industrial equipment including pumps, separators and piping. As with every pumping application, some products work better than others. Barry S. from Bellevue TN illustrates growing customer calls about waste to energy pumps:
“Our client is currently using progressive cavity pumps in a food waste to energy application. The problem is the seafood shells and other abrasive matter are destroying the rotors and costing the facility a fortune in repair costs. They are fed up and want another alternative. You were referred to us by another client who has used your plunger pumps with success for this application and suggested I call you. What we are looking for is a pump than can transfer 160-200 GPM, with an average of 20-30 psi. We have screens on the separators, so much of the abrasives are being filtered out of the process. Other things you need to consider is low ph from the decomposition of the matter in the waste pit. Please have your engineers review this application and let us know your recommendations.” Thanks, Barry S – Bellevue, TN
Barry, the problem with progressive cavity pump rotors is not a new one. They are very costly to replace and abrasive fluids chew them up. This is not a sales pitch but rather a growing response we are getting from both municipal and industrial wastewater treatment operators. What we are recommending for your client is the Sludge Master Plunger Pump PE 943 SS-III which is a type of positive displacement pump called a plunger pump with a space saving configuration.
You mentioned that because the client used a progressive cavity pump initially, there is no concrete pad. This is not a problem. We can design the product with feet to connect directly to the facility floor. We also recommend your customer specifies the pump with chrome oxide plungers to help reduce wear caused by abrasive fluids in the process. The low ph is typically not a problem for this type of positive displacement pumps, We recommend the pump be located closer to the waste pit to maximize the benefit from a gravity feed application.
Related: see pump solutions for food processing applications including food waste to energy