In this guide, we’ll cover everything you need to know to choose the correct diaphragm pump for specific industrial and municipal pump applications. We’ll explain how diaphragm pumps work, what they’re made of, and what they’re used for. We’ll also outline the different types of diaphragm pumps, review the installation process, and discuss routine maintenance – so you can get the most out of your pump.
What is a Diaphragm Pump?
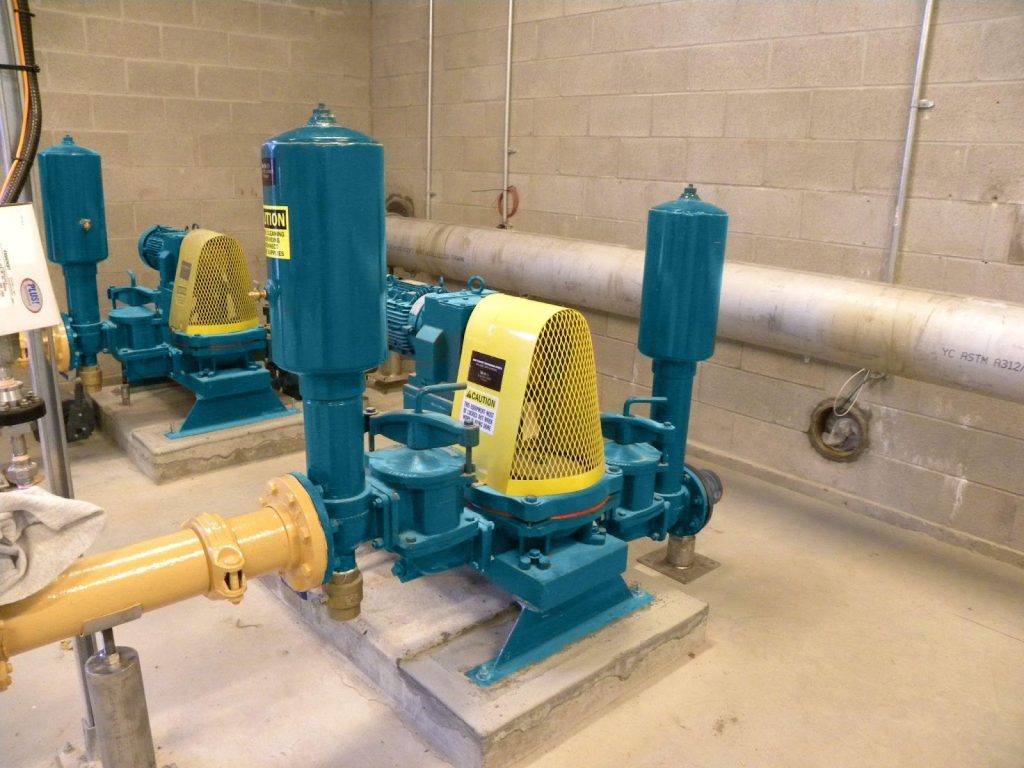
Diaphragm pumps (also known as membrane pumps) are a type of reciprocating positive displacement pump suitable for a broad range of industrial applications. Unlike centrifugal (aerodynamic) pumps, which require an impeller to move liquid through the pump, positive displacement pumps operate using suction. That is, they displace liquid by pulling it into the pump chamber, mechanically or hydraulically moving it through the system, and expelling it. Because they don’t utilize impellers, positive displacement pumps are highly versatile: In many cases, all you need to operate this type of pump is electricity, fuel (gas or diesel) or an air compressor, and they can handle greater variations in pressure, flow rates, and fluid viscosity than centrifugal pumps. They’re also easy to start up, as they don’t require priming or lubrication, which makes them ideal for intermittent use. Mechanical style diaphragm pumps can typically operate dry without damage to the pump. Evacuating air from the hose lines and pump is essential for effective diaphragm pump operation.
Flapper Vs. Ball Valve Diaphragm Pumps
Due to the pumping action of diaphragm pumps, check valves are needed to ensure the liquid inside is pumped in a single direction preventing backflow and potential leaks and contamination. At Wastecorp, our heavy-duty Mud Sucker pumps come with two valve options: Flapper or ball valves. Both pump types are suitable for intermittent use, as they don’t require priming. However, flapper valve pumps are preferred for pumping thinner liquids (those with less than 15% solids), whereas ball valve pumps are the best option for pumping thicker liquids (those with greater than 15% solids) and liquids that dry quickly. Ball valve pumps are capable of breaking up solid material, allowing them to pump highly viscous liquids without clogging.
What Are Diaphragm Pumps Used For?
Diaphragm pumps are designed to handle a wide variety of fluids across a wide range of municipal wastewater treatment and industries to perform numerous essential services. Without them, sanitary sewage, return activated sludge (RAS) waste activated sludge (WAS), food production, waste management, and manufacturing, for example, would be far more costly, risky, and less efficient. Below, we’ll outline some of the key roles diaphragm pumps play in industrial applications:
Municipal Wastewater Treatment
Municipal wastewater treatment plants depend on diaphragm pumps to cost effectively manage their sewage pumping operations. Raw sewage handling applications, thickened sludge pumping, stormwater management, return activated sludge and waste activated sludge operations use time tested diaphragm pumps for both stationary and mobile pumping operations.
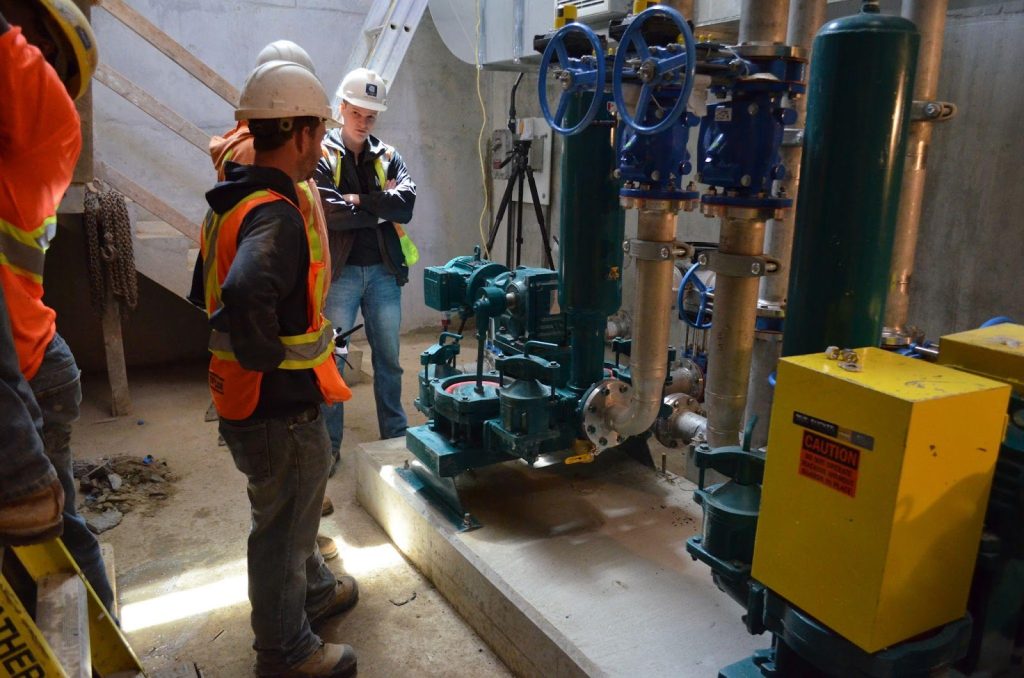
Waste Management
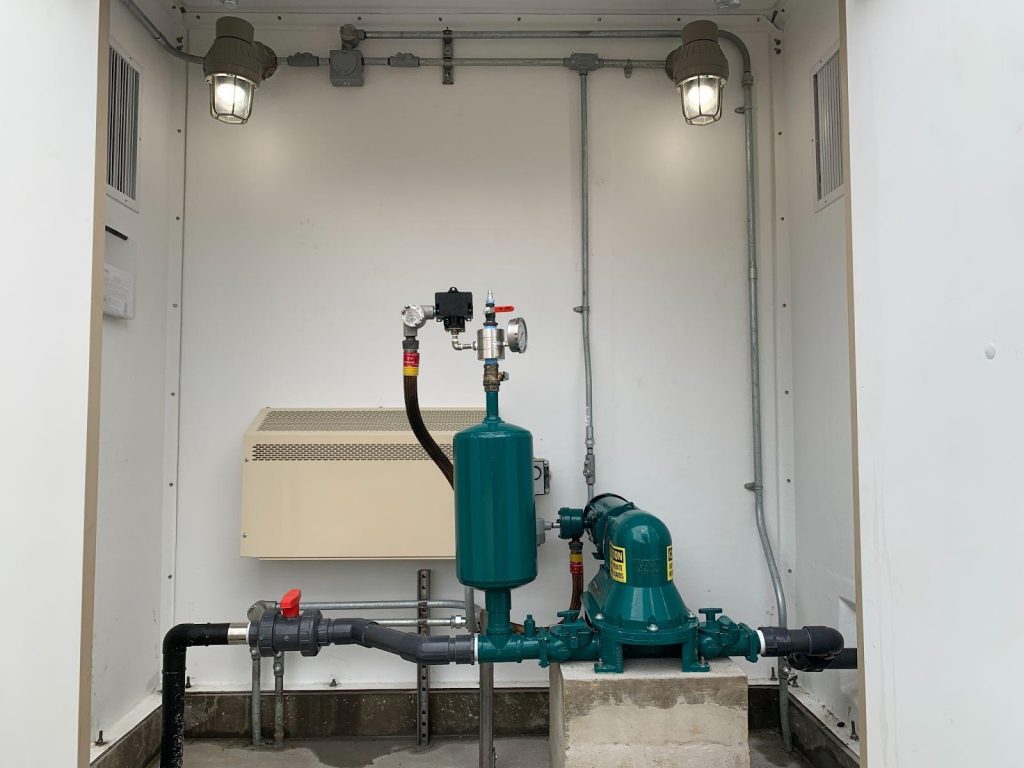
Diaphragm pumps are crucial to managing and reducing multiple forms of waste. In the food industry, diaphragm pumps are used at various stages throughout the conversion of food waste into biofuel (e.g., by moving waste slurry into a heat exchanger and then into an anaerobic digestion facility, where it’s broken down into biogas and fertilizer). This process greatly reduces the amount of food waste entering landfills.
Diaphragm pumps are also used in the safe treatment and management of sewage and wastewater. The excellent sealing ability of high-quality diaphragm pumps, such as our Mud Sucker pumps, makes them suitable for handling all manner of waste without leakage, including tough slurry containing solid waste, mud, and grit. Furthermore, Mud Sucker pumps are built to last, made with durable materials that are resistant to wear, which enables them to pump select corrosive or abrasive fluids. For this reason, Wastecorp pumps have been the preferred choice for municipal sewage and wastewater management in the USA and Canada for over 30 years.
Additionally, Wastecorp is a leading producer of pumps for on-site waste management. Diaphragm pumps, such as our skid-mounted Honey Wagon pump system, are ideal for removing waste from portable toilets, bathroom trailers, and septic tanks.
Food and Beverage Industry
Diaphragm pumps are used extensively to pump poultry, beef, seafood and pork renderings including blood and solids. Diaphragm pumps are also common in breweries and the dairy industry; in addition to pumping milk, they can easily handle semi-solids like yogurt and soft cheese. Diaphragm pumps are also used during the production of chocolate, dough, sauces, cooking oils, and other food items, especially those requiring liquid or semi-liquid additives, such as anti-foaming agents.
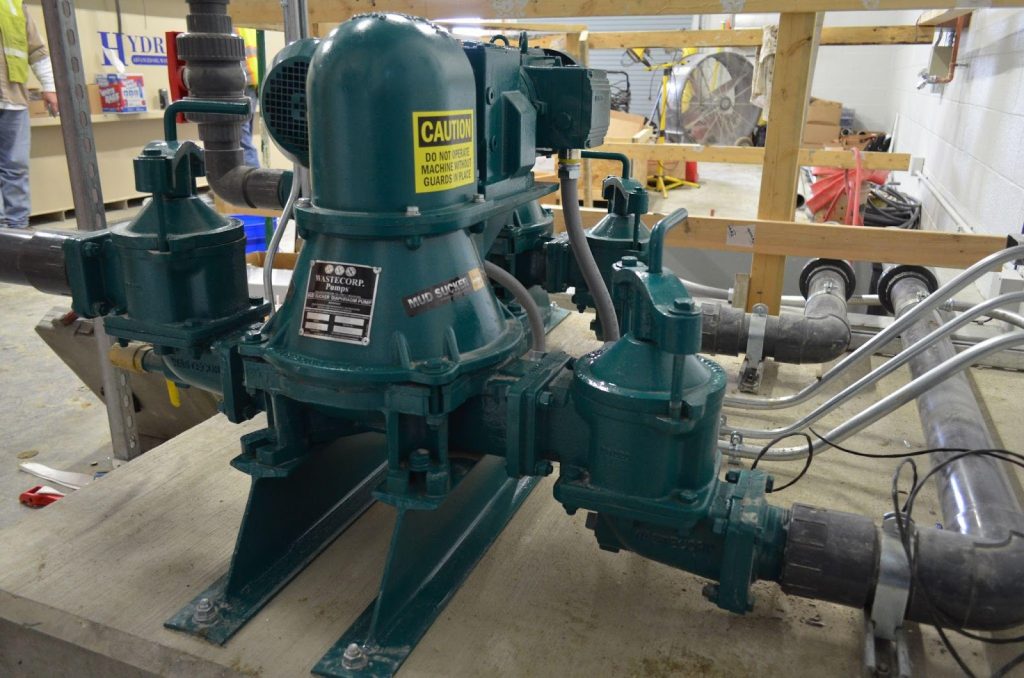
Pool and Spa Industry
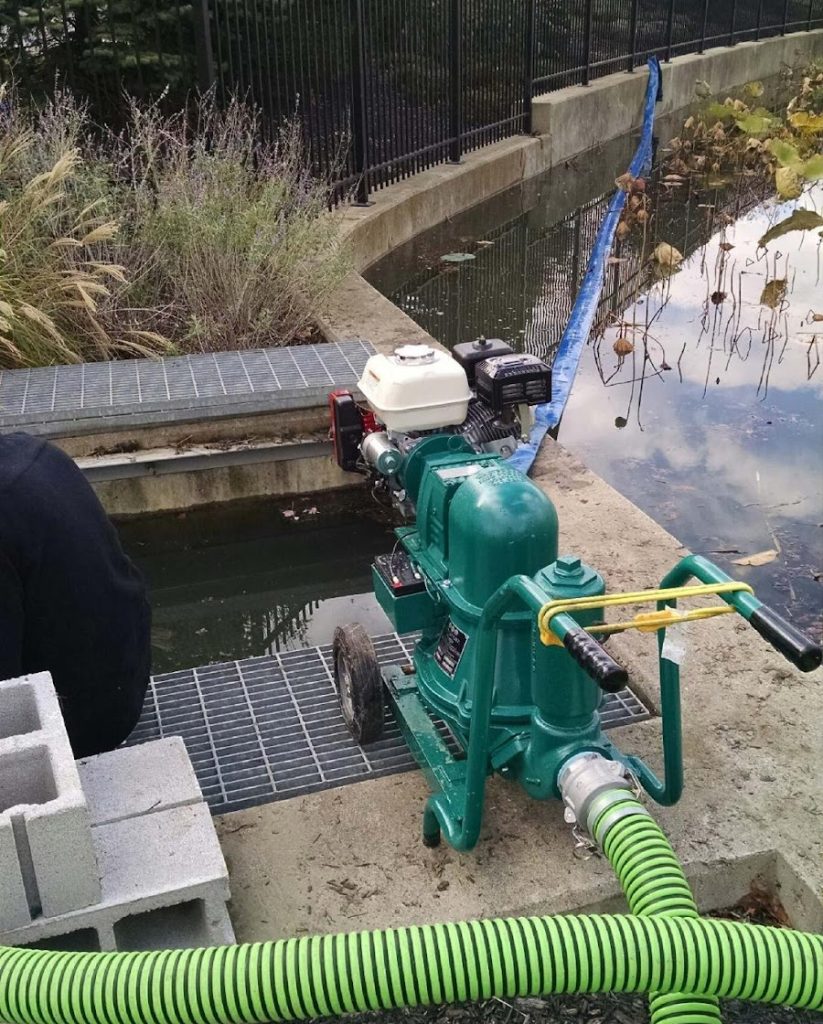
To keep pool and spa environments safe and hygienic, water must be treated with carefully measured doses of chemicals. Diaphragm pumps are integral to this process, as they’re able to precisely deliver controlled amounts of chemical solutions (including corrosive liquids) without leaking or degrading. Due to these features, they can replace the use of peristaltic and solenoid pumps, which are typically used, resulting in a lower cost of ownership for pool and spa maintenance. When opening a pool for the season, diaphragm pumps can effectively pump off the water and debris that accumulates on top of the winter cover including leaves, dirt and wastewater. During pool construction, diaphragm pumps pump aggregate mixed with water, wastewater and solids. It is helpful that diaphragm pumps are available in electric, gas engine and air operated configurations for the pool and spa industry.
Manufacturing
Diaphragm pumps are used during the manufacture of many critical goods, including polymers (e.g., silk, cellulose, rubber, nylon, kevlar, etc.) and paper products. Diaphragm pumps are used to dose ink, paint, liquid resin, and glue to create beautifully finished products, and they’re also used to divert waste liquids post-production. By ensuring these materials are handled safely, diaphragm pumps help prevent environmental contamination during manufacturing due to their seal-less design.
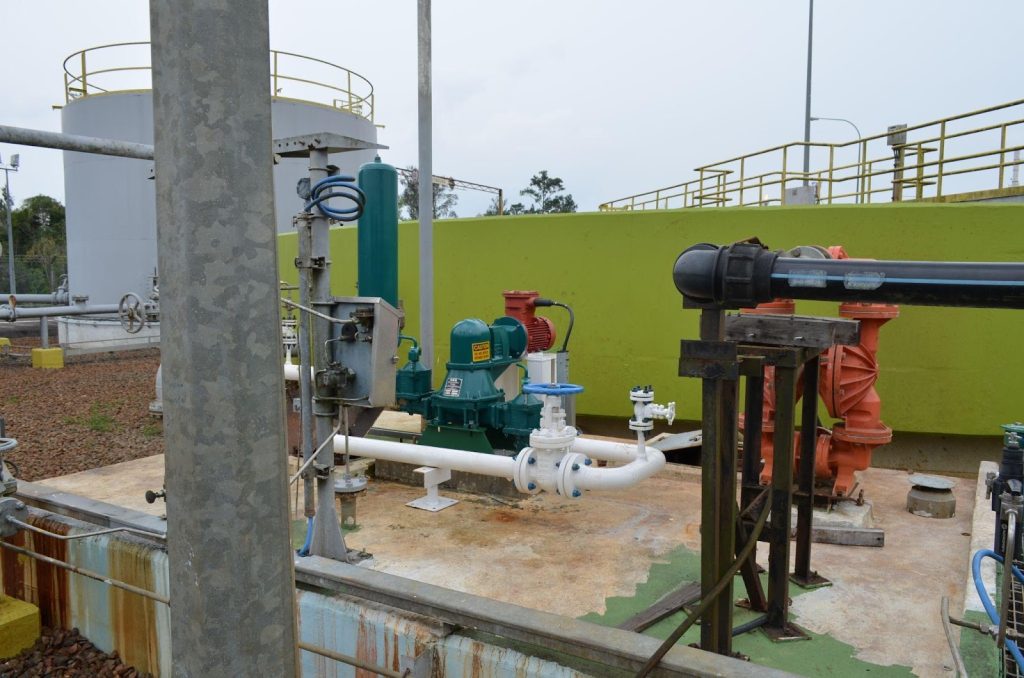
Resource Industries
Diaphragm pumps are pivotal to resource extraction and play a central role in the mining and oil and gas industries. At Wastecorp, we manufacture pumps for use in mining potash (peet), aluminum, bauxite, coal, copper, gold, silver, nickel, chromium, molybdenum, and other essential minerals. Our pumps are used to pump source water, wastewater, and mineral slurry, including slurry with a high percentage of solids. For example, our 4″ Pro Series Engine Diaphragm Pump can process mineral slurry with a solid concentration of nearly 50%, as demonstrated in this case study.
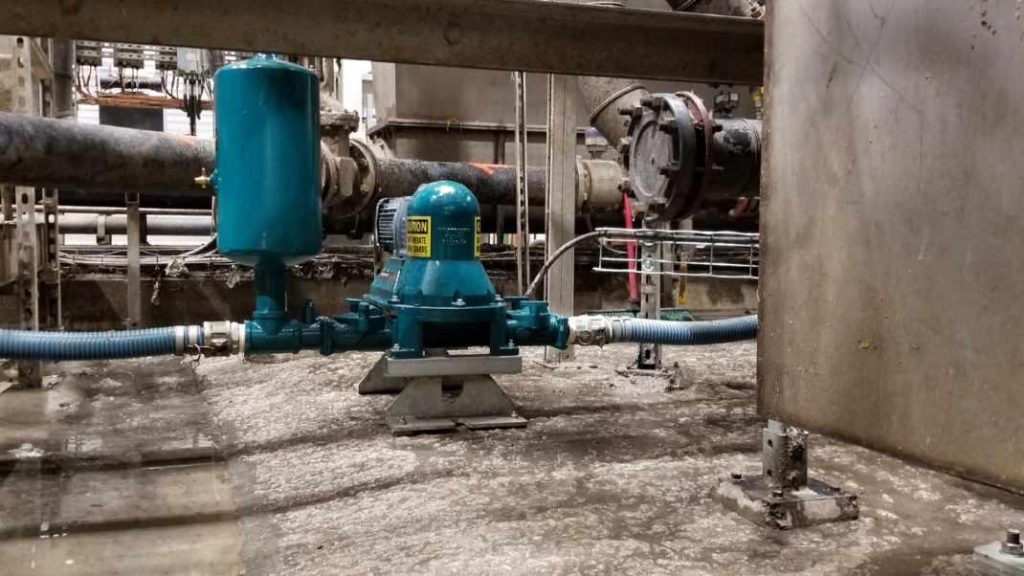
In the oil and gas industry, diaphragm pumps are crucial to almost every step of the production process: They are used to help lubricate oil drilling equipment, transfer crude oil, assist with hydraulic fracking, remove wastewater, and even clean up spills. For example, at Wastecorp, we have created custom-designed Spill Response Pumps that can be deployed quickly to remove spilled oil and solvents, minimizing environmental contamination.
Though these are the main industrial applications for diaphragm pumps, diaphragm pumps are made with housings that can handle all types of fluids . In addition to filling the above roles, diaphragm pumps can also be used during construction, in the marine and railway sectors, the automotive industry, landfill management, power generation, and much more.
Hospitality, Marine and Recreational Industries
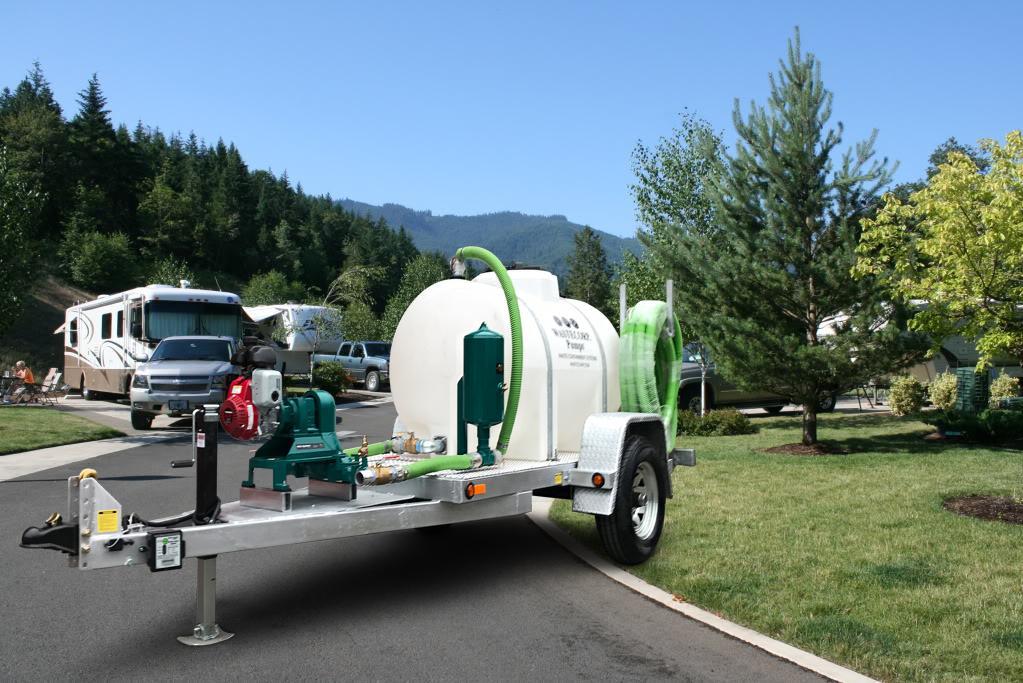
There are two types of diaphragm pumps typically used for pumping out portable toilets, recreational boats and RV’s and campers. The preferred system is called a honey wagon. A honey wagon is a mobile or stationary containment system that includes a polyethylene tank attached to a trailer. A diaphragm pump is connected to the tank via hoses and valves. The diaphragm pump transfers the septic waste, food waste or wastewater into the temporary holding tank for disposal at an authorized dump station like a local wastewater treatment plant at a later time (usually within a few days).
Honey wagons are used by private septic pumping companies who are hired to perform a service. Increasingly, resorts, marinas, hotels, campgrounds, concert venues and parks own their own honey wagon operated by their staff to pump out guest trailers, boats and portable toilets for a fee.
The second method is to use a diaphragm pump to discharge waste directly into the sewer system if available. If no sewer system exists a honey wagon must be used.
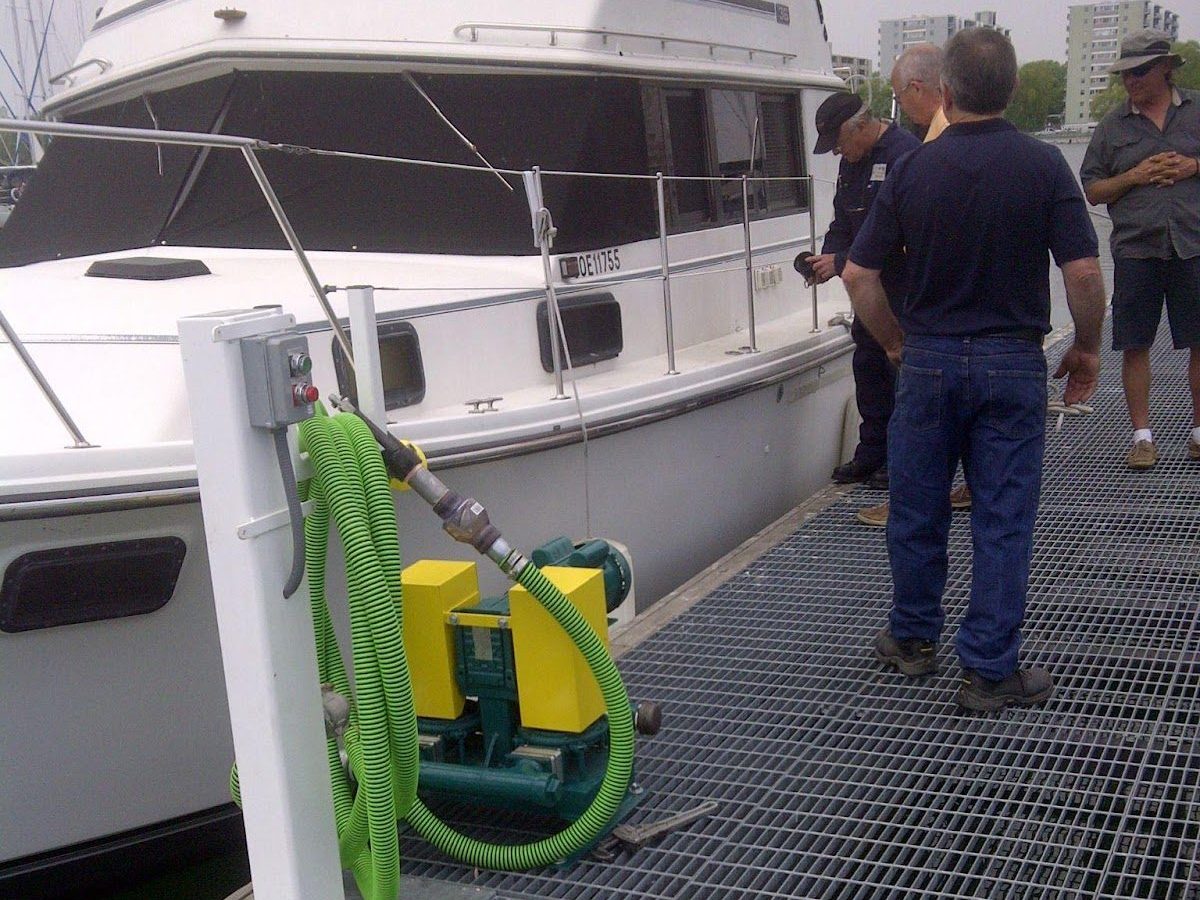
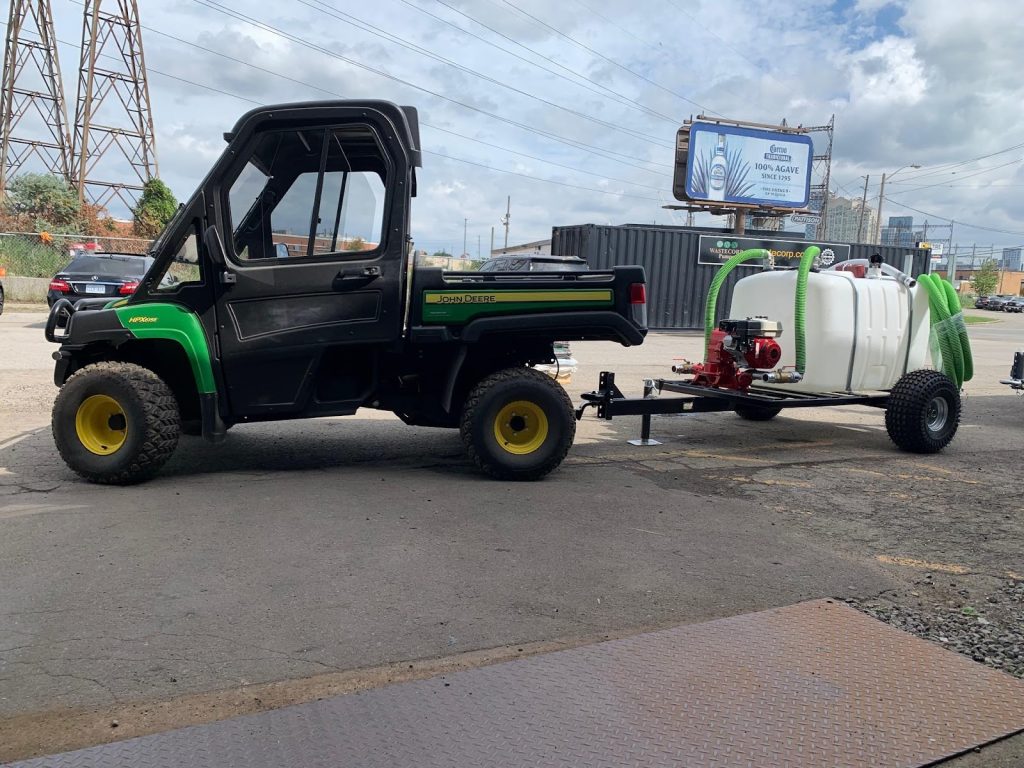
How do Diaphragm Pumps Work?
Diaphragm pumps typically use mechanical or hydraulic forces to suck and discharge a wide variety of liquids. In the case of a double diaphragm pump, for example, two chambers propel liquid using suction created by oscillating diaphragms. Compressed air is directed through a valve at the back of the first diaphragm, causing it to move away from the center of the pump. At the same time, the second diaphragm moves toward the center of the pump, opening up a temporary chamber. Fluid is drawn in to fill the space in the temporary chamber, then the valve of the pump opens, releasing it. To create a vacuum and keep the liquid flowing, the second diaphragm is pushed back in the opposite direction, creating another temporary chamber on the other side of the pump. For as long as the pump is running, the diaphragms continue to alternate back and forth, ensuring continuous pressure.
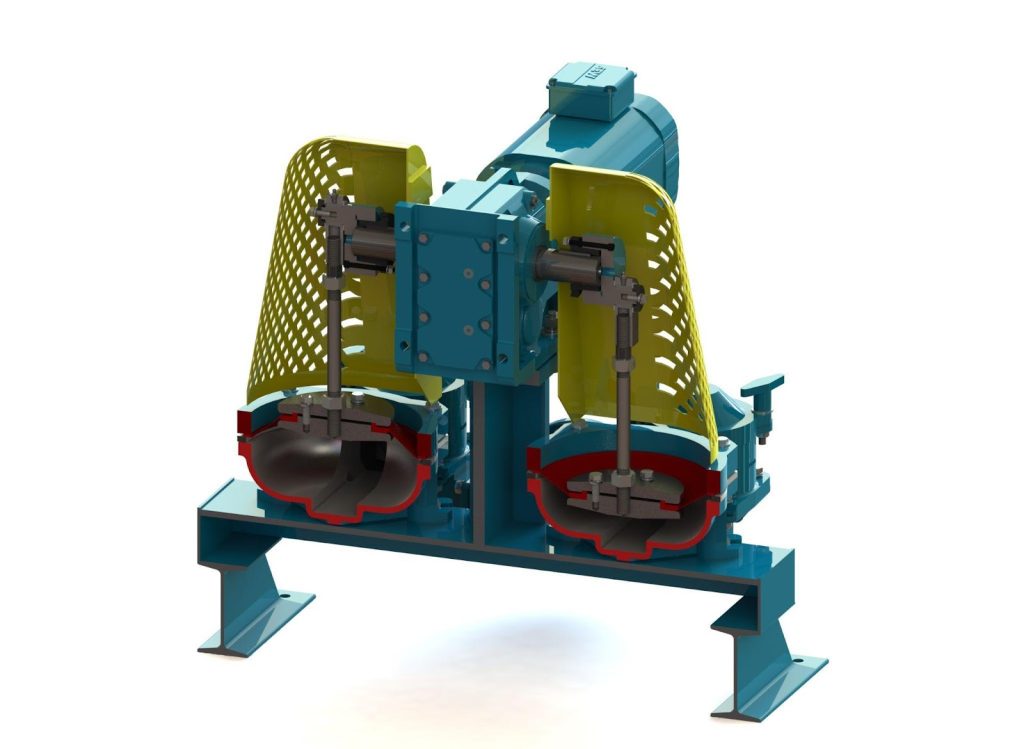
How Does a Diaphragm Pump Work in Terms of Overall Performance?
The exact performance metrics of a diaphragm pump depend on the size and quality of the pump you’re using. As a general guideline, large (4 inch) diaphragm pumps can tolerate a viscosity limit of 50000 CPS under ideal operating conditions and have a maximum flow rate of 280 GPM(1,060 lpm). Some diaphragm pumps can maintain an excellent flow rate even at low pressures, and certain models have a maximum pressure ceiling of up to 125 psi. (Operating a diaphragm pump above 125 psi may result in damage to the unit and is not recommended.) However, it’s crucial to check the performance limits of your specific pump prior to installation and use as pumps vary substantially in their maximum flow rate, psi, and viscosity. Wastecorp Mud Sucker diaphragm pumps are mechanical style diaphragm pumps with operating pressures up to 22 psi.
What Are the Main Components of a Diaphragm Pump?
The main components of a diaphragm pump are as follows:
Pump body
Exclusive to Mud Sucker diaphragm pumps is a suction and discharge area with a patented contoured velocity channel at the bottom of the casting. In general, the central body includes air inlet and outlet valves and a pneumatic exchanger to maintain pressure within the pump.
Fluid (valve) chambers
The fluid chambers hold the liquid being circulated through and out of the pump. They consist of the operator’s choice of flapper valve or ball valve technology to move the fluid.
Manifolds
Manifolds create a seal between the diaphragms and the pump chambers; in some cases, they contain check valves that prevent liquid from flowing backwards.
Air valve
The air valve pushes compressed air throughout the pump assembly, moving the diaphragms and expressing air into the atmosphere to create a vacuum inside the pump.
Diaphragms
The diaphragms act as a barrier, blocking flow through each fluid chamber in succession to maintain suction in the pump.
Air Chambers
The air chambers act as a pulsation dampener when the diaphragm pump is transferring thinner liquids like water. This reduces vibration and “hose kick” when the pump is in operation.
What Are the Main Types of Diaphragm Pump?
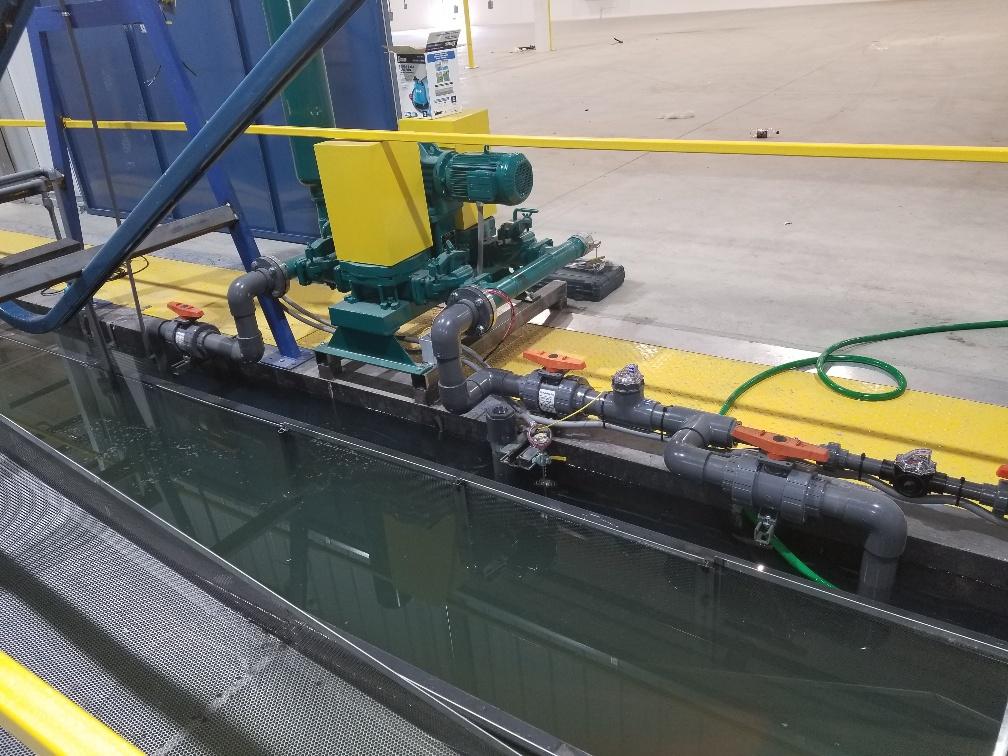
Though there are many varieties of diaphragm pumps in operation today – including custom-designed pumps from diaphragm pump manufacturers like Wastecorp – most applications will use either an mechanical diaphragm pump, AOD and AODD pump, hydraulic diaphragm pump, or electric diaphragm pump(s).
Mechanical Style Diaphragm Pump
Diaphragm Pumps like the Wastecorp Mud Sucker Diaphragm Pump are called mechanical diaphragm pumps. Mechanical diaphragm style pumps are popular for both municipal and industrial fluid handling applications. A mechanical diaphragm pump uses a less complicated flow path to move fluid from the suction to the discharge side of the pump with the simplest fluid handling channel possible. Mechanical diaphragm pumps are also available with a wider selection of drive systems like electric, gas, diesel, explosion proof, air and hydraulic. Mechanical diaphragm pumps have become more popular among engineers and operators for their energy saving reputation and their ability to pump high-viscosity fluids, including sludges, slurries, abrasive liquids, and shear-sensitive fluids.
Air Operated Double Diaphragm Pumps (AODD)
Air operated diaphragm pumps are another popular type of diaphragm pump. AODD pumps (also known as pneumatic pumps) use compressed air to move the two flexible diaphragms back and forth, pushing liquid through two pumping chambers. Each chamber has a discharge check valve, a diaphragm, and a suction check valve, while compressed air is supplied via an internal distribution system.
AODD pumps are used in many industries because they’re durable, versatile, and easy to maintain. However, AODD pumps are more prone to vibration and pulsation than other diaphragm pumps, so they typically require a pulsation dampener. AODD pumps are also only suitable for use with low-pressure applications, and they’re prone to icing up, which limits their functionality in cold environments.
AODD pumps are the preferred choice for use with many high-viscosity fluids, including sludges, slurries, abrasive liquids, and shear-sensitive fluids.
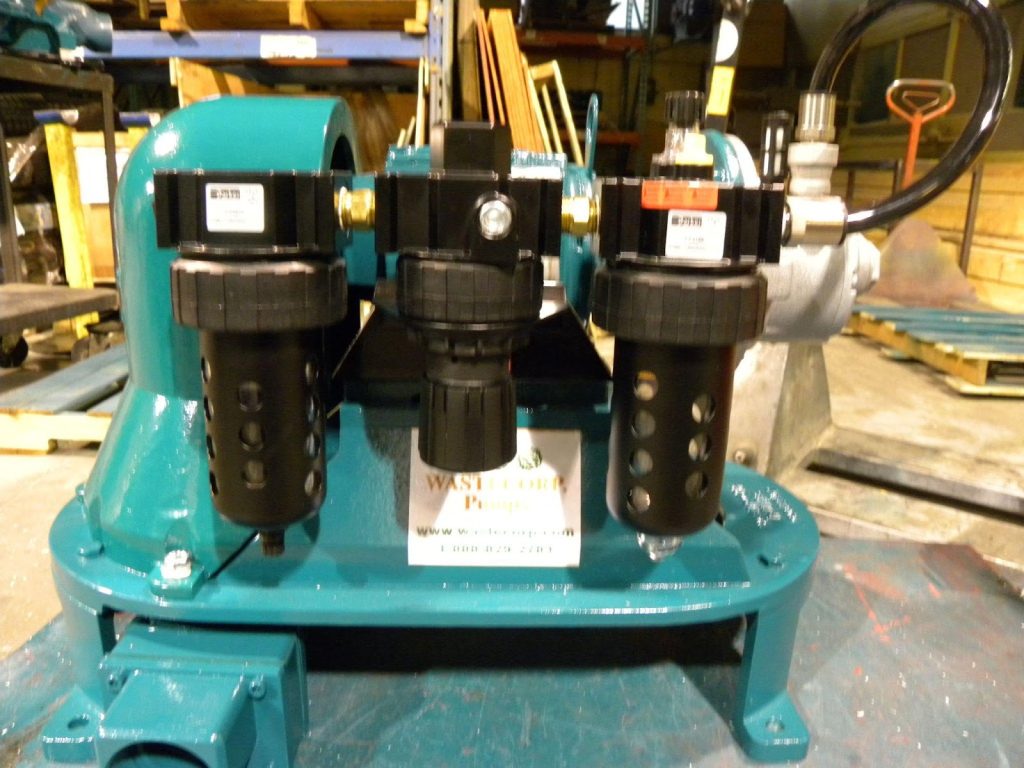
Hydraulic Diaphragm Pumps
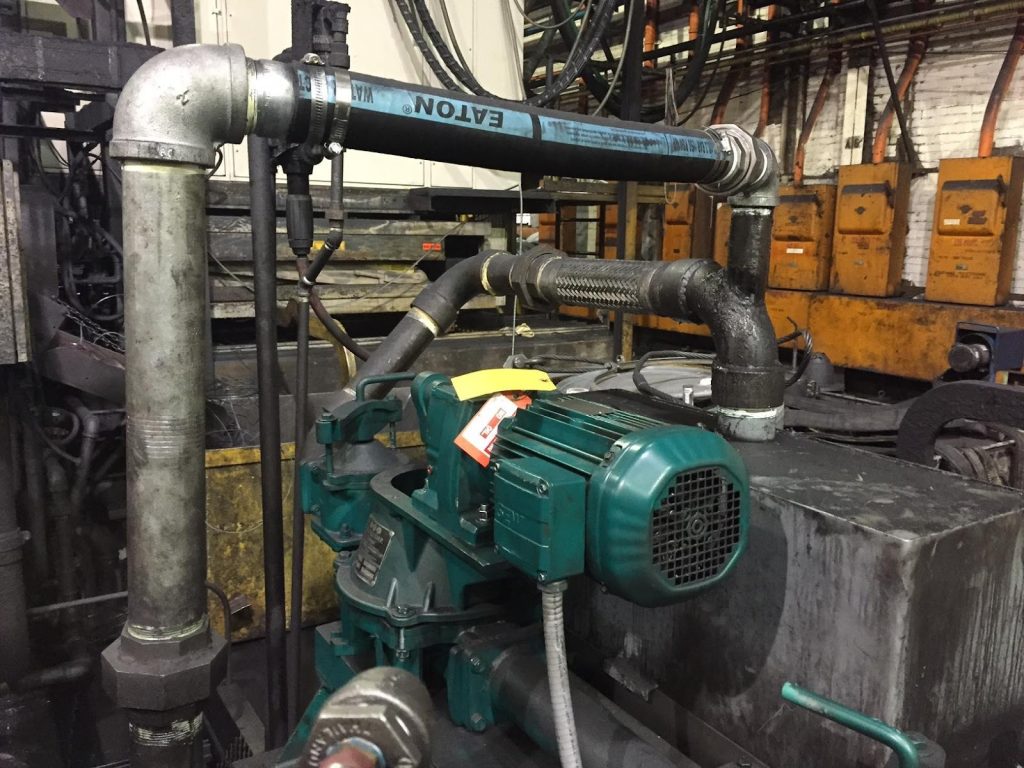
Hydraulic diaphragm pumps use hydraulic fluid rather than electricity, fuel or compressed air to move the diaphragms. This system allows them to control high flow rates and handle high pressures (the hydraulic fluid creates counter-pressure, protecting the pump). These qualities make hydraulic pumps an excellent option for working in the oil and gas industries .
Electric Diaphragm Pumps
Electric diaphragm pumps use an electric drive motor coupled to a gearbox to drive the diaphragms rather than compressed air. Typically, these pumps employ a central cam and roller system which moves the diaphragms back and forth in a very smooth, linear motion, greatly reducing pulsation. As such, these pumps are recommended for applications where quiet operation is a priority. They’re also a good choice for high-pressure applications, having a psi range of 60-100.
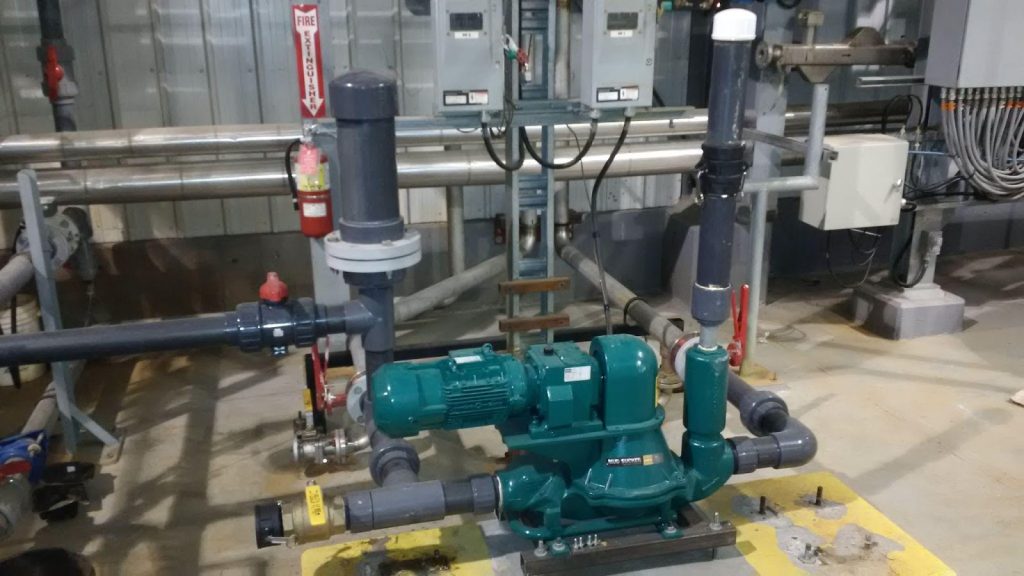
Other benefits of electric diaphragm pumps include:
Ability to stall under pressure, which prevents the pump from becoming damaged if it clogs.
Energy efficiency. Electric pumps can be up to 80% more energy-efficient than AODD pumps.
No need to install a pulsation dampener.
Excellent flow control. Many electric diaphragm pumps can be programmed to dispatch a specific amount of liquid, either by controlling the flow rate or dosing batches.
Versatility. Electric diaphragm pumps can be used with a wide range of chemicals, corrosives, shear-sensitive liquids, and slurries.
What’s the Difference Between a Single Diaphragm Pump and Double Diaphragm Pump?
As their names suggest, single diaphragm pumps contain just one diaphragm wet section, while double diaphragm pumps contain two wet sections. Though both pump types can move liquid effectively, single diaphragm pumps are much more prone to flex fatigue and produce larger “pulses” during operation. These issues occur because the single plate is installed in a fixed (captive) position and pumped up and down repeatedly, which increases wear and tear on the pump. In double diaphragm pumps, the two plates gently flex back and forth. Likewise, single diaphragm pumps have difficulty handling thick slurries or liquids that contain solids because their ball check valves are susceptible to clogging.
Single diaphragm pumps can be a good choice for temporary applications involving low-viscosity fluids, but for most industrial operations, double diaphragm pumps are the better option. Wastecorp allows you to configure your pump with either single or double diaphragms, depending on your needs.
What Materials are Diaphragm Pumps Made of?
High-quality diaphragm pumps, like Wastecorp’s Mud Sucker pumps, incorporate multiple materials carefully chosen to suit various applications and handle a variety of fluids. Before purchasing a diaphragm pump, consider the type of liquid(s) you intend to handle and then select a pump with the correct materials, using the information below as a reference:
Diaphragms, Ball Valves, Seals
The flexible components of diaphragm pumps are made of either durable rubber compounds or thermoplastic materials:
Rubber Materials
Neoprene: Neoprene is affordable and long-lasting, but has limited chemical resistance. The best choice for most non-chemical applications; e.g. pumping water slurries.
Nitrile (BN): Nitrile has more chemical resistance and is typically used when pumping oils and hydrocarbons.
FKM Fluorocarbon (VT): FKM has superior resistance to chemicals, but loses flexibility faster than many other rubber materials, resulting in a reduced lifespan. Best for caustic chemical applications and use with acids.
EPDM (ND): Balances acceptable chemical resistance with durability and enhanced performance in low temperatures. A good choice for use with less-caustic chemicals or diluted acids.
Thermoplastic Materials
Santoprene (EPDM/Polypropylene cross-linked): Santoprene is one of the best diaphragm pump materials available thanks to its unique combination of excellent resistance to chemicals and abrasives and its exceptionally long flex life. Santoprene is suitable for use with oils and other petrochemicals while offering superior durability. At Wastecorp, we use Santoprene in many of our heavy-duty Mud Sucker pumps to ensure long service life.
Hytrel (FDA): Hytrel is a very smooth material suitable for food processing applications as it can easily be cleaned and kept hygienic.
Fluid Chambers, Manifolds, Seats, Diaphragm Plates
The rigid components of diaphragm pumps are made from either metal or hard plastic:
Metal Materials
Aluminum: Aluminum offers moderate chemical resistance while being lightweight and strong. It’s a good choice for use with paint and petrochemicals and many mining applications. At Wastecorp, we use heat-treated aluminum to enhance the strength and durability of our pumps.
Cast Iron: Cast iron is stronger and more resistant to abrasion than aluminum, but it’s much heavier. As such, its use is typically limited to stationary applications.
Stainless Steel: Stainless steel is very smooth and has excellent chemical resistance, making it a popular choice for food processing.
Alloy C: Alloy C is highly resistant to chemicals but very costly. Choose alloy C if you plan to work with very caustic chemicals or undiluted acids.
Plastics
Polypropylene: Polypropylene has moderate chemical resistance suitable for use with many acidic and caustic liquids; it’s also lightweight and highly affordable.
PVDF: PVDF offers superior chemical and abrasion resistance (compared to polypropylene), making it one of the best choices for use with high-concentration chemicals and acids.
Unlike many diaphragm pump manufacturers, Wastecorp collaborates with clients to build custom pumps, ensuring each pump is ideally suited to its intended purpose. If you have questions about which materials you should select for your pump, feel free to contact us by phone at 1-888-829-2783. We’ll be happy to help you find or create the perfect pump for your application.
How to Properly Install a Diaphragm Pump
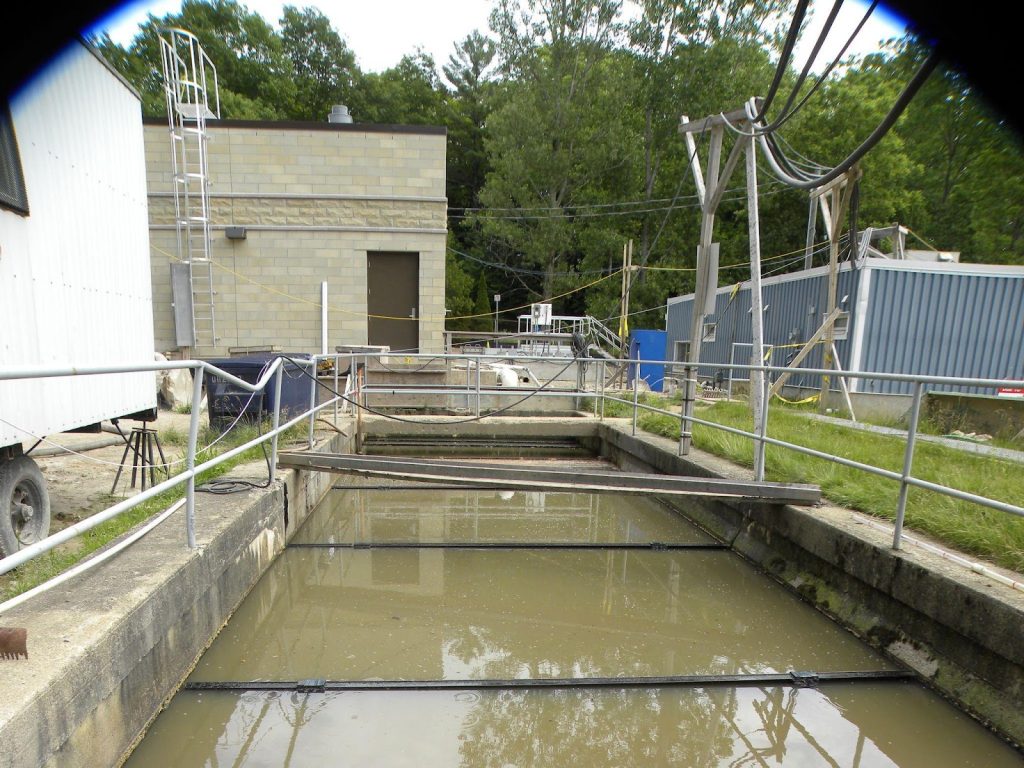
Diaphragm pumps are relatively simple to install and operate, but several best practices must be kept in mind during installation. To prevent damage to your pump, make sure you:
– Mount the pump to a rigid baseplate.
– Avoid reducing the suction port size.
– Never use a pipe or hose that’s smaller than the suction port size.
– Use the shortest suction pipe or hose possible; ideally, suction pipes and hoses should never be more than 5 meters long.
– Make sure your pump has an air filter/regulator installed.
– Regulate the air pressure to 2 bar the first time you start up the pump.
– Try to maintain a cycle speed of 60 to 70 cycles per minute (doing so reduces energy usage and prevents premature wear and tear).
– In some cases, such as when a pump is going to be fully submerged in water or when split suction is required, installation techniques may differ. It is important you consult your user manual for detailed installation instructions specific to your model of diaphragm pump or contact Wastecorp for assistance.
How to Maintain a Diaphragm Pump
Routine maintenance can greatly extend the lifespan of your diaphragm pump and prevent clogging and other problems on the job.
Take the following steps during usage to keep your pump running smoothly:
– After each use, inspect your pump for signs of wear or clogging. If you notice scratches inside the pump, you may need to install a back pressure device to protect the diaphragms during high-pressure applications. If you see bubbling or signs of deterioration and you’ve been using caustic chemicals or acids, your pump is likely suffering from chemical damage. Remove the pump from operation and select a model with materials suitable for use with potent chemicals and acids.
– Always keep the pump well-lubricated (if using a pump that requires oil), as doing so will prevent wear and keep the pump running as efficiently as possible.
– Thoroughly clean the pump after each use to remove chemical residue and dirt.
– Use screen filters, if needed, to prevent sharp debris from entering the pump.
– If your pump clogs, inspect the air valve and muffler for dirt, corrosion, or damage. Clean or replace these parts as needed.
– If your pump is overly noisy or you notice inconsistent flow, install a pulsation dampener.
– Never run a pump in which the diaphragms have become damaged; doing so can severely harm the pump system.
To prevent your pump from freezing, try the following tips:
– Clean the muffler (if dirty) or choose a different muffler material.
– Alternatively, add a rubber extension hose to the pump.
– Add a dryer to the compressor system to reduce moisture levels.
– Reduce the speed and pressure of the pump.
– Install a straight exhaust pipe to reduce the risk of freezing in the pipe bends.
– Use one exhaust with one exhaust port instead of multiple exhausts.
Replacing Parts on a Diaphragm/Double Diaphragm Pump
Having to occasionally replace parts is a normal part of the lifecycle of diaphragm pumps. Most manufacturers recommend replacing the diaphragms in pumps after 300-500 hours of use, and the valves and seals should be replaced after 1000 hours of use.
High-quality diaphragm pumps have a lifespan of 30 years or more. As such, it’s unusual to have to replace the entire unit; most diaphragm pump problems can be prevented or solved with routine maintenance and repair. The only exception to this rule is when pumps are severely damaged during use, such as when a pump is run with broken diaphragms. To service your diaphragm pump, consult the manual that came with your pump, or contact Wastecorp at 1-888-829-2783. We sell complete diaphragm pump repair kits and offer on-demand repair services.
Additionally, Wastecorp stocks a full range of replacement parts for our Mud Sucker line of pumps, as well as parts compatible with other major diaphragm pump manufacturers, including rare and hard-to-find items, such as parts for discontinued CH&E Diaphragm Pumps.
Advantages and Limitations of Diaphragm Pumps
While diaphragm pumps are useful for a broad range of applications, there are certain situations where centrifugal pumps are still a better choice. Understanding the features and limitations of diaphragm pumps is key to selecting the correct type of pump for your purpose.
Advantages of Diaphragm Pumps
– Handle high-viscosity (thick) liquids well, including liquids with a high percentage of solids.
– Easily handle corrosive and abrasive fluids when manufactured with the right materials.
– Operate more effectively at high pressures or low flow rates than centrifugal pumps.
– Offer greater accuracy when measured doses of liquid are required for an application.
– Can maintain a consistent flow even with variations in pressure.
– Will not damage shear-sensitive liquids.
– Self-priming, which is ideal for applications with intermittent flow.
– Diaphragm pumps are portable and submersible, giving them greater versatility than centrifugal pumps.
Disadvantages of Diaphragm Pumps
– Have reduced pumping power (compared to centrifugal pumps) when working with low-viscosity liquids. As a general rule, if the fluid you wish to pump is under 200 Cp viscosity, you should use a centrifugal pump.
– Have a lower overall flow rate than centrifugal pumps, making them a poor choice for some spraying applications.
– Diaphragm pumps are typically noisier than centrifugal pumps and can be more susceptible to wear and tear. Choosing a high-quality pump with a pressure relief system is of particular importance when using a diaphragm pump. Centrifugal pumps, on the other hand, are simple to operate and do not require a pressure release system. For this reason, they’re the preferred choice when pumping low-viscosity, low-shear liquids, such as water.
Conclusion
Diaphragm pumps play an essential role in many industries due to their durability, power, and versatility. Able to handle a wide range of challenging liquids (including caustic chemicals and oil, thick slurries, liquids requiring mechanical separation, wastewater and sludge), diaphragm pumps are an integral tool for making everyday operations safer and more efficient.
Whether you’re in the oil and gas industry, construction, the food and beverage industry, agriculture (or aquaculture), or seeking a way to manage municipal or on-site waste, Wastecorp pumps are an excellent choice. Our ready-made and custom double diaphragm pumps have been trusted internationally for over 30 years, making them the gold standard for industrial use. Our pumps are highly versatile, leak-proof, durable, and efficient.
If you aren’t sure which diaphragm pump is right for the job you have in mind, we can help: Contact Wastecorp today for a free assessment to find the best pump to meet your needs.
Frequently Asked Questions (FAQs) on Diaphragm Pumps
What’s the purpose of a pump being able to self prime?
Non-self-priming pumps must be placed above the level of liquid, which can allow air to enter the line, creating a risk of overheating. Self-priming pumps avoid this issue by releasing air from the line before liquids are moved.
What’s the best pump for a sprayer?
Centrifugal pumps are the best choice for low-pressure, high flow-rate applications that do not involve highly caustic liquids. They’re also capable of mixing liquids with wettable powders, which is necessary for some agricultural tasks. Diaphragm pumps are better suited to high-pressure applications, or applications where separation between the liquid and the pump components is needed, such as when handling highly corrosive chemicals.
What type of motor is a diaphragm pump?
Electric diaphragm pumps typically contain either a brush DC motor or a brushless DC motor. Brushless DC motors are the best choice for pumps that will be run continuously for very long periods.
Can you run a diaphragm pump dry?
Yes, most diaphragm pumps can be allowed to run dry for limited periods without sustaining any damage. However, it is not recommended to allow diaphragm pumps to run dry for long periods. Consult your pump’s manual for details on intermittent operation.
Why are AODD pumps ideal for chemical transfer?
AODD pumps are ideal for chemical transfer because they’re leak-proof and don’t generate heat, which makes them a safe choice for use with harmful or potentially flammable fluids. They’re also suitable for intermittent use, chemical-resistant, and capable of handling a wide range of viscous and corrosive liquids.
What parts of the pump can be customized?
At Wastecorp, we allow clients to customize a wide variety of pump parts so they can create the perfect diaphragm or centrifugal pump for their desired application. Some examples of pump parts that can be customized include vacuum options, mounting options, control configuration, motor options, connection size, and speed control. Some pump models also come with options for extra accessories, such as hoses, handles, air chambers, float and pressure switches, strainers, and valves. Using these accessories, one pump can be adjusted to suit several different applications.
What’s the difference between a diaphragm and piston pump?
Instead of using flexing diaphragms to propel liquid through the pump, piston pumps utilize one or more pistons which move inside dedicated chambers. The pulling action of the pistons draws liquid into the chambers, while the pushing action of the pistons expels it. Piston pumps offer very smooth, consistent, and powerful performance, but they’re less durable than diaphragm pumps and less capable of handling high-viscosity fluids.